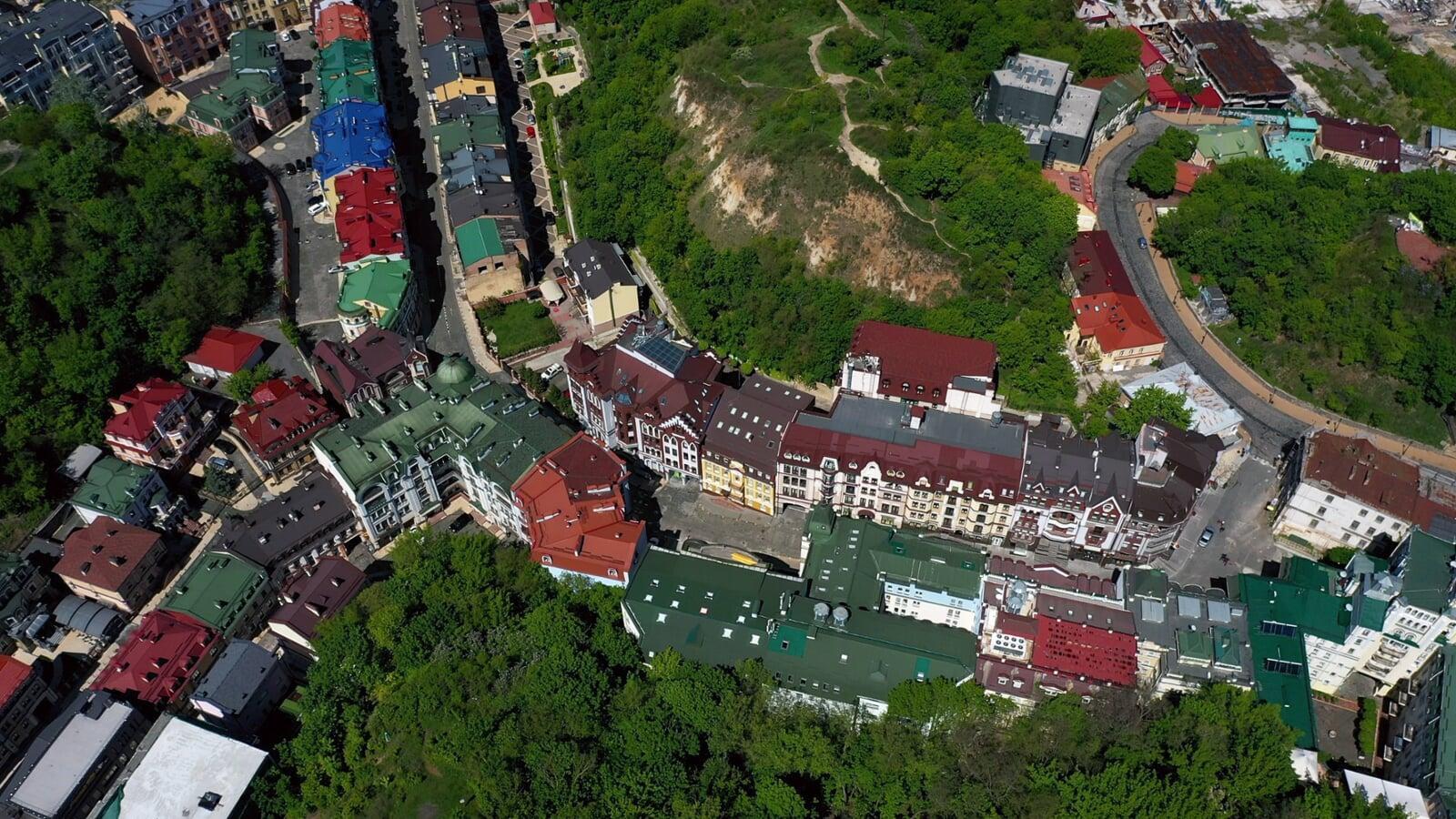
1. What Are Factory‑Built ADUs?
2. Why They're Trending Now
2.1 Speed & Predictability
Build timelines are slashed by 40–60 %, with on-site final assembly taking just weeks.
Strict factory workflows and weather-independent schedules improve reliability.
2.2 Cost Savings
Bulk materials and efficient labor reduce prices by up to 20–40 % vs. traditional builds.
Fixed pricing minimizes unexpected overruns.
2.3 Sustainability
Waste is cut by 30–50 %, material usage is optimized, and carbon impacts are reduced.
Prefab units often incorporate energy-efficient designs—and can be outfitted with solar and smart tech.
2.4 Quality & Precision
Standardized inspections and factory conditions ensure higher consistency and lower defects.
2.5 Minimal On-Site Disruption
Most building happens off-site, cutting noise, dust, and neighborhood disturbances.
3. Real-World Examples & Pricing
Business Insider highlights Bay Area startup Villa, building 440–1,200 sq ft prefab ADUs for $95,000–$180,000—installed in under 90 days.
Bay Area Perpetual Homes starts at mid‑$200k (500 sq ft) and mid‑$300k (1,200 sq ft) delivering eco-friendly, turnkey ADUs.
Reddit data show modular ADU costs range from $150k–$250k, with timelines between 8 weeks and 6 months—versus 12+ months for stick-built.
4. Emerging Trends in Factory-Built ADUs
Smart Integration: Automated lighting, climate control, security, and voice-enabled systems are going mainstream.
Adaptive Design: Foldable layouts, transformable spaces, and multifunctional furniture meet diverse lifestyle needs.
Advanced Materials: Use of cross-laminated timber, recycled steel, and low-VOC finishes improves durability and appeal .
Off-Grid Viability: Plug-and-play solar, battery, and greywater systems make many prefab ADUs self-sustaining.
5. Benefits & Challenges
Benefits | Challenges |
Faster completion & fewer delays | Transportation logistics & permits |
Predictable, transparent pricing | On-site utility & foundation prep |
Superior, consistent quality | Less design flexibility |
Eco-friendly practice & materials | Aligning factory and field teams |
Minimal disruptions locally | Sizing limits for modules |
6. How to Get Started
Assess Your Site: Ensure access for delivery truck, space for crane, and utility hookups.
Choose a Provider: Seek prefab ADU manufacturers with certifications, warranties, and green credentials.
Design & Permitting: Engage early for designs that meet local codes and factory standards.
Parallel Workflows: While prefab is built, complete site prep (foundation, utilities).
Install & Finish: Coordinate timely installation, inspections, and final touches.
Maintain: Follow a maintenance plan for systems like HVAC, solar, and smart tech.
FAQ
Final Takeaway
Factory-built ADUs represent a transformative leap in backyard housing—faster, greener, cost-effective, and tech-forward. With streamlined production and installation, homeowners can unlock additional space, income, and sustainability, often in under half the traditional time. Considering a backyard build? Factory-built ADUs are fast becoming the go-to solution.
Related Articles:
How to Get an ADU Permit in Escondido